Injected polyamide
Dimensions : 813 × 606 × 552 mm
Vitra, SwitzerlandVitra (International) AG
Klünenfeldstrasse 22
CH-4127 Birsfelden
T +41 61 3770000
F +41 61 3771510
www.vitra.com
Growing a Chair
Ronan & Erwan Bouroullec
The initial intuition was that of a chair which would sprout up like a plant. A vegetal chair, its branches gently curving to form the seat and back. It comes from this fascination we have for various types of old furniture, which is plant-inspired. Garden chairs of English origin, structured in boughs of cast iron, for example; various items formed using real branches; or even those armchairs designed in the United States during the first half of the
last century, using bushes whose growth had been restricted until they took on the form of a chair. Objects which, in short, take us back to a time when forms were perhaps a little bulkier, less sleek or smooth than nowadays. There was therefore, from the outset, a desire to create an original structure, based on a complex and narrative form of construction. Coupled with an inclination for highly advanced techniques, such as plastic injection moulding, which opens the way to mass distribution.
The initial designs show a chair that has the fluidity and uniform elegance of a plant: a great unity of form whilst at the same time being, in essence, untamed.
They immediately appealed to Rolf Fehlbaum, but their complexity posed the question of industrial feasibility. This led to the start of close collaboration with the team led by Egon Bräuning, head of the development department, which was to last almost four years.
The main issue was to follow the realistic geometry of a chair, whilst at the same time using the principles of plant-like branching as a construction model. What we felt was possible in order to maintain the integrity of our proposed design was approached in stages, whilst asking questions about its compatibility with the manufacturing process. Take Algues for example, developed by Vitra in 2004. Its branching form was shown to be particularly suited to the requirements of plastic injection moulding. This process consists of injecting the liquid material, under very high pressure, into a steel mould. Just like the sap in a tree trunk, it has to circulate evenly inside all the branches of the mould, congeal and then solidify — and all in less than two minutes, at the end of which the piece is extracted. The major difficulty with this process resides in the alchemy which has to take place between the material, how quickly it moves, the fall in its temperature and its method of solidification. In other words, there is a certain number of uncertainties to grasp, given that the result must be perfectly uniform.
One of the important stages in the process consisted in transforming the branch sections, circular at the outset, into a T-profile. This solution gives better structural qualities whilst at the same time meeting the demands of injection fluidity. As luck would have it, it turned out that this solution reinforced the plant-like aspect of the whole piece.
Throughout the entire duration of the project, the only way of conducting an in-depth study into industrial feasibility was to represent the chair by means of our virtual modelling software, that is, an orthonormal digital script, which represents an obstacle to the refined chaos of the organic. Resorting to this working method, which consists of moving on from a drawing to three-dimensional representation, is unremitting. Here, we found a subterfuge: having produced drawings by hand on large sheets of paper on a ı:ı scale, these two-dimensional designs were projected onto the surface of a shell. On the seat and the back, this worked fairly well, as the drawing of the branches does not move too much. Instead, there was serious distortion on the slope of the armrests. Like an anamorphosis. The distortion of the design, when applied to the form in three dimensions, was a real surprise. The branches had to be redesigned. But the real difficulty lay in retaining their spontaneous aspect. The great ambiguity of this project was to make the very sophisticated technique demanded by plastic injection moulding cohabit with a necessary poetry that can only be obtained through the sensitivity of drawing by hand.
Plastic chairs usually fall within two distinct groups: either the shell is fixed to the base, or the entire chair is moulded in a single piece. In the case of Vegetal, the solution adopted was different. For better stability, the front legs are linked to the shell. In a certain way this causes them to be much more in line with the design of the chair. At the back, the legs are glued on. These are two separate parts. Then there was the issue of successfully incorporating them in a way that is fluid, but also structured. It was decided to branch out the circular sections of the legs to make them match up with the T-profile sections of the seat, the objective being to retain the suggestion of an organic development.
As well as the two- and three-dimensional design drawings, throughout the duration of the work process, models have enabled the changes made to be visualized spatially. This part of the work was, on the one hand, carried out on very precise models, manufactured by Vitra, and, on the other, on items modelled by us, more sensitively. During the past year, when the process was speeding up, we were designing directly on to the models provided by Vitra, in order to perfect the position of each branch and the accuracy of its curve.
Vegetal could not have existed without the technical sophistication of modern software, in the same way that it could not have moved on from the finesse intrinsic to the stages of design drawing by hand. It is the close association of these two processes that has been so special. The complexity of its form, which must be uniform as a tree or a flower would be, has continuously forced us to rethink the whole thing in respect of each detail: one might say, this chair has been redesigned a thousand times.
Interview with Constance Rubini, January 2009.
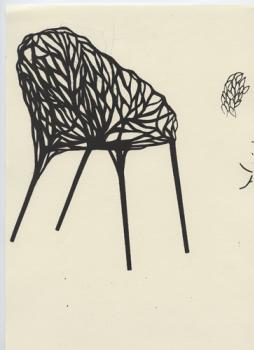
©Ronan et Erwan Bouroullec
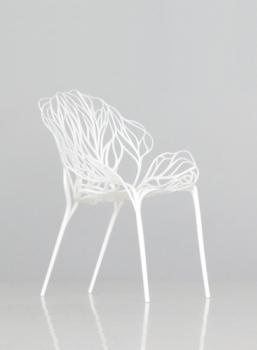
©Ronan et Erwan Bouroullec
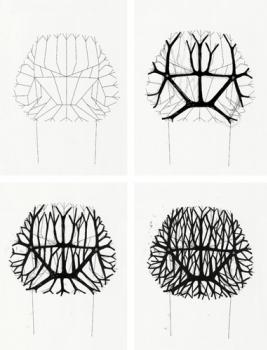
©Ronan et Erwan Bouroullec
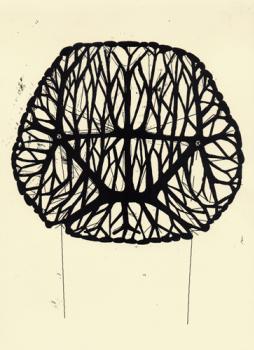
©Ronan et Erwan Bouroullec
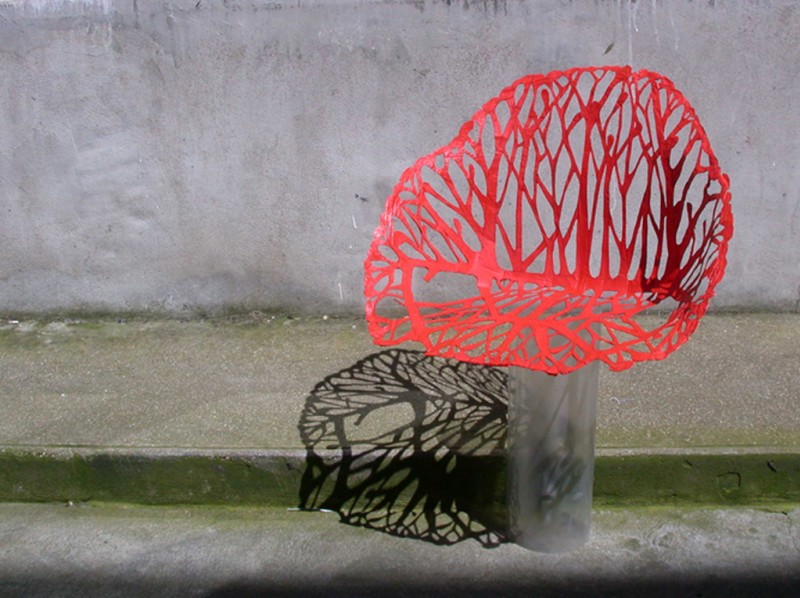
©Ronan et Erwan Bouroullec
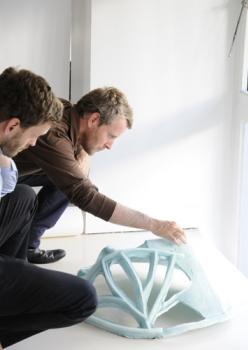
©Ronan et Erwan Bouroullec
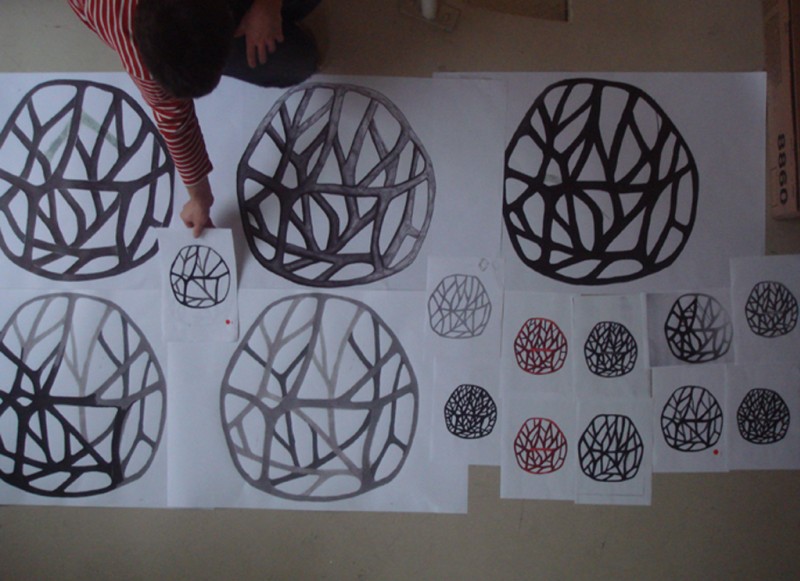
©Ronan et Erwan Bouroullec
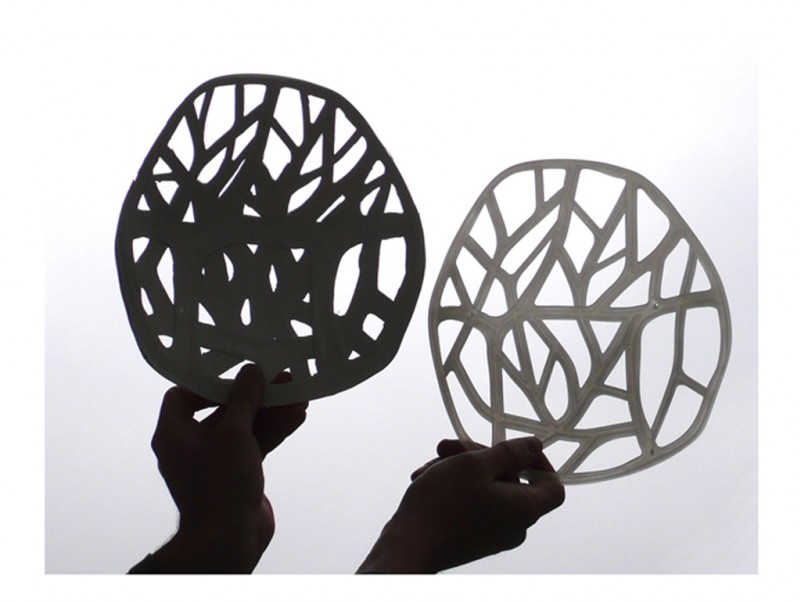
©Ronan et Erwan Bouroullec
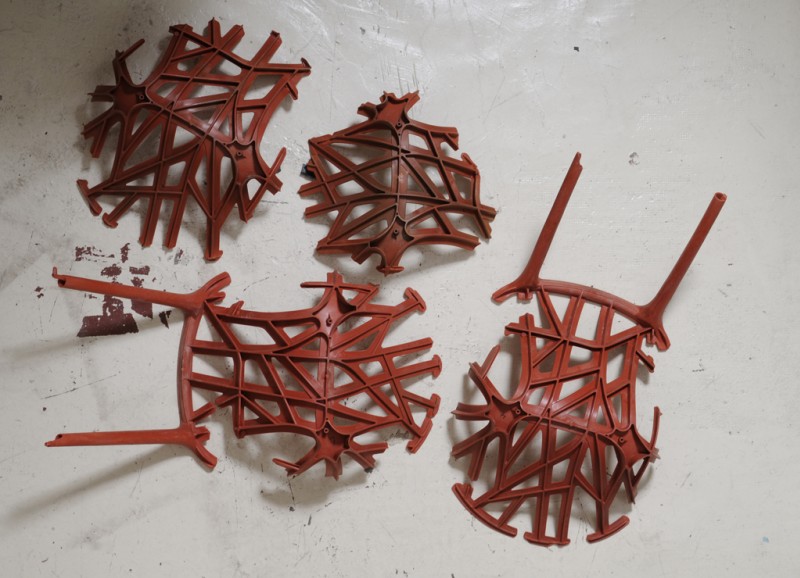
©studio Bouroullec
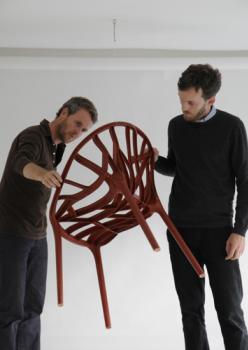
©Ronan et Erwan Bouroullec
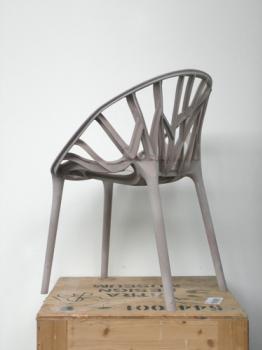
©Ronan et Erwan Bouroullec